Broken Bullbar Bolts
Submitted: Wednesday, Oct 13, 2021 at 18:53
ThreadID:
142711
Views:
7582
Replies:
9
FollowUps:
20
This Thread has been Archived
Phil G
Anyone had the bolts break on their bullbar and if so what do you think caused it?
I have a 2019 Troopy fitted with a popular Australian commercial steel bullbar (I don't like naming brands but it is not ARB).
It developed a squeak so I thought I'd
check the bolts and found that the heads of 6 of the M10 8.8 tensile bolts had broken off.
I took the bullbar off and found the 6 broken bolts were not actually clamping metal to metal - there was a 2mm gap between bullbar and chassis when the bolts were done up tight so the bolts were straddling a gap rather than clamping the bullbar to the chassis rail.
The bolts were always torqued to spec - when I fitted it myself and probably sometime since.
My only interest is to fix it and prevent it happening again. I do my fair share of corrugations - the vehicle has done the Canning, the ABH and lots of dirt road trips in outback SA, Qld and NSW.
Anyway I bought new bolts from Hobson to replace all the Chinese bolts and made up steel shims to space out the gaps between the bullbar mounts and chassis rails, so the bolts are doing their job.
Anything else I should do?
Reply By: RMD - Wednesday, Oct 13, 2021 at 20:01
Wednesday, Oct 13, 2021 at 20:01
G'day Phil.
Just curious as to how there is a gap there now, which you have shimmed, but wasn't it there at time of fitting? If the bolts are from that "special supplier", maybe the quality although 8.8 , may
well be less tensile than expected. Given the twist of chassis and localized stress at bolt heads maybe they, one at a time decided to let go as each took the stress in turn. Pull on 1 spot weld and it lets go and then the next etc,
If the bolts had little or no radius at the shank to head, ie, very abrupt and square, then they will likely fail as they are flexed, even tensile ones.
AnswerID:
638279
Follow Up By: Phil G - Wednesday, Oct 13, 2021 at 20:39
Wednesday, Oct 13, 2021 at 20:39
I fitted the bullbar when the Troopy was new - just followed the instructions to the letter. No shims.
The gap made the fitting really easy!! Slid straight on.
Yeah my first though was the bolts were no good - the head said JL brand 8.8 tensile - so I looked them up and they are a chinese bolt supplier so thats when I though I'd use an Australian brand I trusted and bought Hobson. The bolts I had to drill out were very easy to drill!!!
On my last trip we did a bit of 4wding over soem rocky tracks and I rember hearing a bang but not knowing what it was - I guess might have been a bolt letting go.
FollowupID:
916648
Follow Up By: Allan B (Sunshine Coast) - Wednesday, Oct 13, 2021 at 22:23
Wednesday, Oct 13, 2021 at 22:23
.
There was a gap at the time of fitting. Phil said... "there was a 2mm gap between bullbar and chassis when the bolts were done up tight"
FollowupID:
916651
Reply By: Keir & Marg - Thursday, Oct 14, 2021 at 10:05
Thursday, Oct 14, 2021 at 10:05
Plenty of info on the interwebby about mild steel versus high tensile steel. Here's an extract. Note the last sentence.
"What is High Tensile Steel?
High tensile steel is a type of mild carbon steel which has a high yield strength and tensile strength. It contains different alloying elements in order to increase the tensile strength of the steel. These elements include chromium, nickel, molybdenum, silicon, manganese and vanadium.
Moreover, it has considerably high fatigue strength and toughness as
well. However, it shows a reduced plastic ductility and brittle fracture compared to many forms of mild steel."
AnswerID:
638283
Follow Up By: Zippo - Thursday, Oct 14, 2021 at 12:27
Thursday, Oct 14, 2021 at 12:27
" it shows a reduced plastic ductility and brittle fracture compared to many forms of mild steel."
That's where I was going to suggest earlier that the problem may lie. If Phil still has the failed bolts ("machine screws"?) or at least the heads, brittle fracture has a tell-tale appearance.
[Bolts vs machine screws: when I went through engineering, machine screws were all thread, and bolts were not. Maybe the terminology has gone fuzzy or merged since then. I know calling them all bolts is easier though.]
FollowupID:
916659
Follow Up By: Peter_n_Margaret - Thursday, Oct 14, 2021 at 13:45
Thursday, Oct 14, 2021 at 13:45
" it shows a reduced plastic ductility and brittle fracture compared to many forms of mild steel."
I am no specialist in this subject, but if a piece of metal is being flexed to the extent that its fatigue life becomes an issue, it is too weak for the job it is doing.
A bigger bolt or a higher tensile bolt (or both) will improve its life, in my view.
Cheers,
Peter
OKA196 motorhome
FollowupID:
916660
Follow Up By: RMD - Thursday, Oct 14, 2021 at 14:57
Thursday, Oct 14, 2021 at 14:57
I agree with Zippo, the suitability of Set screws/machine screws against actual bolts is probably the issue. If, through chassis twisting repeatedly, the bolts, not really bolts, will break seeing Phil has said the thread went to near the heads, Certain to fail. As Zippo mentioned, the fine grained fatigue break face tells a story of the type of failure. Someone mentioned about shear forces, Unlikely to be ANY shear forces unless hitting things, ie, Roos. unless it was the last few bolts flogging in the holes. The bolts certainly didn't shear. I am surprised the captive nuts held on to allow the fixing bolts to break just outside the chassis. Indicates bend forces repeatedly causing cracks and failure. He is lucky it is a heavy chassis, as many earlier BT50's and Rangers developed loose bolts for some reason and the bolts which held on simply fatigued the chassis and broke bits out of the chassis.
A conrod bolt has shank all the way through both halves and is ONLY threaded in the last mm or so where NO flex, only tension happens. It not like that they do not survive. Some I fitted to large machinery engines were not tightened to a torque, but "Free and Tightened length difference was the way they achieved uniform tension/tightness, ie, degree of Yield.
FollowupID:
916661
Follow Up By: Phil G - Thursday, Oct 14, 2021 at 16:24
Thursday, Oct 14, 2021 at 16:24
Just remembered I had two photos. And yes, shearing forces were not part of it as the intact bolts would have prevented any shearing. All broken bolts were coming from the sides. Intact bolts were pointing to the rear
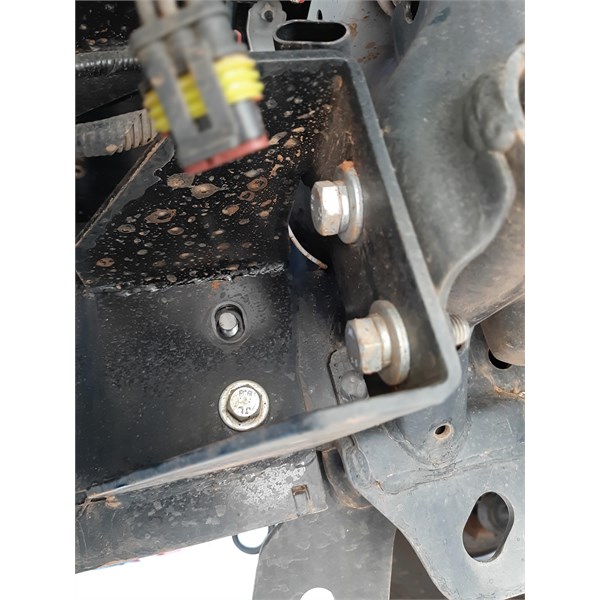
Bolt with broken head
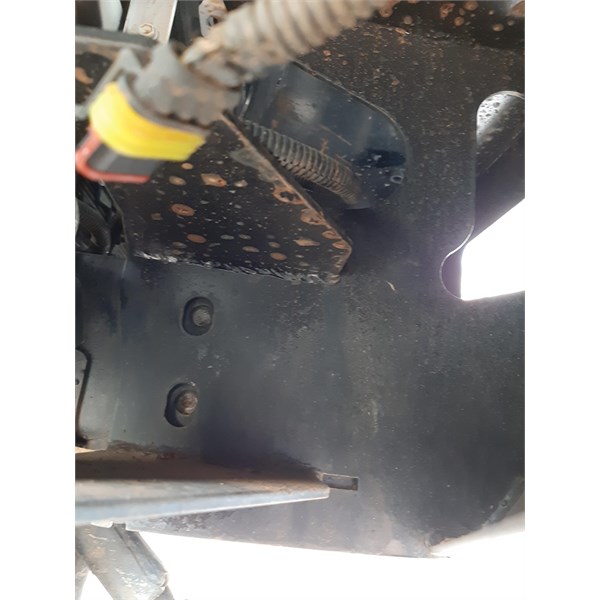
Broken bolts on right hand side
FollowupID:
916663